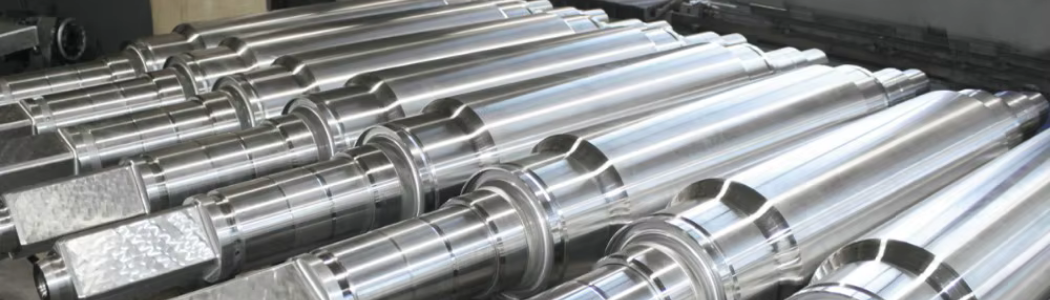
HSS Rolls / Rings
HSS Rolls Production Cycle
1. Material Selection: The production of HSS rolls starts with selecting high-quality steel alloys, typically containing elements like tungsten, molybdenum, chromium, vanadium, and carbon, which contribute to the roll’s hardness, wear resistance, and ability to withstand high temperatures.
2. Melting: The raw materials (scrap metal and alloying elements) are melted in an electric arc furnace (EAF) or induction furnace. This process ensures that the material is free of impurities and provides a uniform molten metal base.
3. Casting: After the metal is melted, it is cast into the shape of a roll in a mold. The roll’s size is determined by the specific requirements of the steel mill. In some cases, the casting process might involve continuous casting, where the molten steel is poured into a mold and continuously solidified into a desired shape.
4. Forging: Once the cast roll cools and solidifies, it is forged to refine the grain structure and enhance mechanical properties. Forging involves applying pressure to the cast roll to improve its strength, toughness, and uniformity.
5. Heat Treatment: To achieve the desired hardness and wear resistance, the forged rolls undergo heat treatment. This typically involves processes like quenching (rapid cooling) and tempering (controlled reheating), which harden the steel and enhance its resistance to high-temperature deformation and wear.
6. Machining and Finishing: After heat treatment, the rolls are precision-machined to the correct dimensions. This includes turning, grinding, and polishing to ensure smooth surfaces and dimensional accuracy. These processes also ensure that the rolls will function correctly in rolling mills.
7. Inspection and Testing: The finished rolls undergo stringent quality control checks to verify their mechanical properties, surface quality, and dimensional accuracy. This includes hardness testing, ultrasonic testing, and sometimes x-ray inspection to detect any internal defects.
8. Shipping: Once the rolls pass all quality checks, they are shipped to customers in the steel and iron industries for use in rolling mills.
Chemical Composition of HSS Rolls
The chemical composition of High-Speed Steel rolls is designed to maximize hardness, wear resistance, and thermal stability. A typical HSS roll will have the following chemical elements:
• Carbon (C): 0.7% – 1.2%
Carbon is a key element that influences the hardness and wear resistance of the roll.
• Chromium (Cr): 4% – 6%
Chromium enhances hardness, wear resistance, and corrosion resistance.
• Tungsten (W): 6% – 18%
Tungsten contributes to high-temperature hardness and helps maintain the roll’s strength under extreme heat in rolling mills.
• Molybdenum (Mo): 2% – 5%
Molybdenum increases toughness and hardenability, especially under high-temperature conditions.
Vanadium (V): 1% – 5%
Vanadium increases the strength and wear resistance of the material and contributes to fine grain structure.
• Nickel (Ni): 0.5% – 2%
Nickel can improve toughness and strength, especially in high-temperature environments.
• Silicon (Si): 0.2% – 1.0%
Silicon helps in increasing strength and heat resistance.
• Manganese (Mn): 0.5% – 2%
Manganese improves hardness, toughness, and wear resistance.
• Phosphorus (P) and Sulfur (S): Usually kept very low (typically less than 0.02% each)
Both phosphorus and sulfur are considered impurities in HSS rolls as they can negatively impact toughness and corrosion resistance.
This composition ensures that HSS rolls have excellent mechanical properties, high wear resistance, and the ability to withstand the extreme temperatures and pressures encountered during rolling operations.