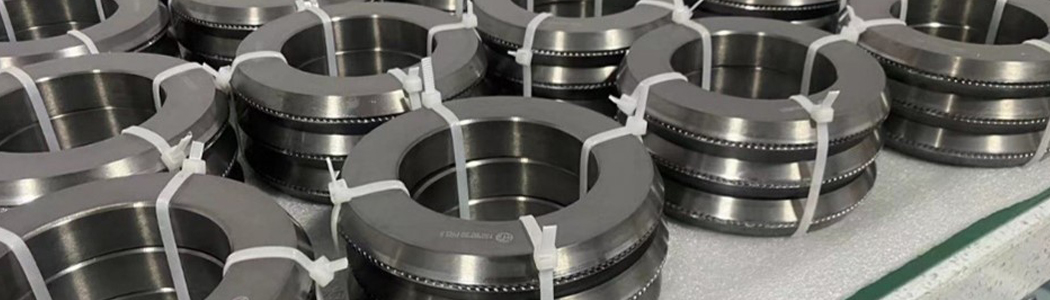
Tungsten Carbide Rings
Producing Tungsten Carbide (WC) carburized rolls for the steel industry involves several key processes, as these rolls are essential for handling the high temperatures, pressures, and wear conditions in steel mills. Tungsten carbide is favored because of its hardness, wear resistance, and ability to withstand high thermal stresses, making it ideal for rolls used in the production of steel.
Here’s a general overview of the process for producing Tungsten Carbide carburized rolls:
- Roll Design and Material Selection
- Roll Core Material: Tungsten carbide rolls typically have a steel core (commonly high-quality tool steels, such as 100Cr6, 60NiCrMoV8, or similar materials) that is carburized to provide strength and toughness. The outer surface is coated or treated with a tungsten carbide layer for wear resistance.
- Carburizing Steel: Choose a high-carbon steel or alloy with a good balance of toughness, hardness, and machinability to form the core of the roll.
- Tungsten Carbide Powder Preparation
- Powder Selection: Tungsten carbide is usually produced by mixing tungsten metal powder (often with a small amount of carbon) with a binder metal (like cobalt or nickel) to form a powder.
- Powder Mixing: The powder mix is processed to achieve a homogenous blend. The binder ensures that the tungsten carbide particles can be sintered (fused together) into a solid material.
- Molding and Shaping
- Roll Shape Creation: The shape of the rolls is typically made using a powder metallurgy process. The steel core roll can be preformed using machining or casting techniques, while the tungsten carbide material can be shaped by pressing or injection molding to fit around the roll’s surface.
- Cold Isostatic Pressing: After shaping, the WC powder is subjected to cold isostatic pressing (CIP) to compact the powder into the desired shape. This process helps to create a dense and uniform material.
- Sintering
- Sintering Process: The compacted tungsten carbide is sintered at high temperatures (usually above 1,400°C) in a vacuum or hydrogen atmosphere to remove impurities and create a solid carbide phase. This process fuses the tungsten carbide particles together, giving the material its hardness and wear resistance.
- Cobalt Binder: The binder metal (often cobalt) helps to hold the tungsten carbide grains together, providing some ductility and toughness to the final product.
- Roll Carburizing Treatment (for Steel Core)
- Carburizing the Steel Core: The steel core roll is subjected to a carburizing process, in which carbon is diffused into the surface of the steel to form a high-carbon layer (a hardened case) that improves the wear resistance and hardness of the roll. This process involves heating the roll in a carbon-rich environment (e.g., a furnace with a controlled carbon atmosphere).
- Heat Treatment: After carburizing, the steel core is typically quenched and tempered to achieve the desired mechanical properties, including hardness, toughness, and stress resistance.
- Coating the Roll with Tungsten Carbide
- Plasma Transferred Arc (PTA) or Laser Cladding: After the carburizing of the steel core, a tungsten carbide coating is applied to the surface using techniques like plasma transferred arc (PTA) welding or laser cladding. These processes involve fusing a layer of tungsten carbide onto the steel core, creating a hard, wear-resistant surface.
- Fusing Tungsten Carbide Powder: During the cladding process, tungsten carbide powder is introduced into the molten pool created by the arc or laser, and the carbide is melted and fused to the steel surface.
- Thickness Control: The tungsten carbide layer typically ranges from 2 mm to 10 mm in thickness, depending on the application and the wear requirements.
- Post-Processing
- Machining: After cladding, the rolls are often machined to ensure they are within the specified dimensions, smooth surface finish, and proper tolerances. This may involve grinding or turning to ensure the proper roll profile and surface quality.
- Surface Polishing: Some rolls may require additional polishing or honing to improve the surface finish and reduce friction during the steel forming processes.
- Quality Control
- Inspection: The finished rolls undergo rigorous inspection to ensure they meet the required standards for hardness, wear resistance, dimensional accuracy, and surface quality.
- Non-Destructive Testing: Methods like ultrasonic testing or x-ray inspection can be used to detect internal defects such as cracks or voids in the tungsten carbide layer or the steel core.
- Final Testing and Shipping
- Roller Testing: The rolls may undergo simulated tests to verify their performance under actual operational conditions, including heat cycling, load testing, and wear testing.
- Shipping: Once the rolls pass all tests and inspections, they are shipped to steel mills for use in rolling operations.
Conclusion
The production of tungsten carbide carburized rolls involves a combination of advanced manufacturing techniques such as powder metallurgy, sintering, carburizing, and cladding to create a high-performance product capable of withstanding the harsh conditions of the steel industry. These rolls offer exceptional durability, wear resistance, and heat resistance, making them critical components in steel rolling processes.